Healthcare’s savior may be manufacturing!
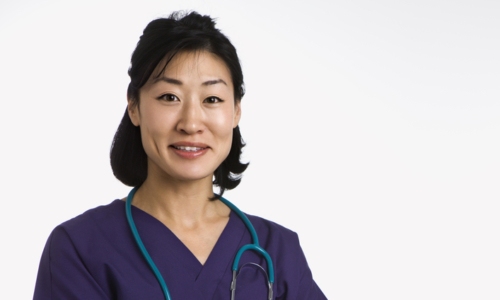
What can Healthcare learn from Manufacturing?
A topic we all know and hear about on a daily basis is the high cost of healthcare. Yet, the US has one of the greatest healthcare systems in the world and when the idea of socializing it comes up, there is revolt. Rightly so, as there are many issues with those systems. But just maybe there is a way to make an impact without revolutionary change.
The US manufacturing industry is one of the best in the world and capable of amazing things. Most notably is quality and cost. US Manufacturing delivers high quality and low cost in almost every sector of manufacturing regardless of product or constraints. So how do they do it? There is a constant focus on the system to continuously improve and look for new and innovative approaches.
Three powerful tools that are used are observation, benchmarking and data analysis. Briefly here is what they entail:
Observation- is just simply standing in the midst of a process and “seeing” (Gembutsu) what is really going on and constantly asking the question “Why?”. So many significant improvements have been made by just watching and then acting. The key is to look for waste.
Benchmarking- is observation in an external sense. Going out and seeing what others are doing and then applying them to a new environment but similar challenge. It is said that the gravity feed racks in supermarkets were the impetus of the wide use in auto assembly.
Data analysis– is the statistical evaluation of data in regards to the whole process including the output results. Yes, I know there is “HIPA”. But data can be sterilized and does not necessarily need to include intimate health details.
So, what should be done? Every US healthcare facility should begin to ask itself how can we lower the per patient cost. Here is what I mean by that. In a typical doctor’s office, the visit process looks like the following:
Check in, wait, ushered to room, screening, wait, doctor exam, wait, release to front desk, payment or next appointment. What is the cost associated with each of these steps? Yes, waiting costs money (chairs, floor space, insurance, etc.). Once quantified work can begin to reduce the costs while maintaining the quality of care or even enhancing it. This is just a simple example of the approach and how to examine costs in a process.
SPC Consulting works with physicians, office managers and others on how to identify, quantify and reduce their operation costs and improve the profit. Call us today to learn more.